You'll spot quality pottery by examining five key features with your eyes and hands. Start by checking the visual appearance under bright light, looking for even glazing and authentic handmade marks. Feel the weight and density – good pottery should feel substantial and balanced, with higher-fired pieces making a clear ring when tapped. Examine the glaze for smoothness and consistent coloring, without defects like pinholing. Check for expert craftsmanship through symmetrical rims, well-crafted handles, and stable bases. While these basics will help you identify quality pieces, there's so much more to discover about pottery's intricate details.
The Importance of Visual Inspection
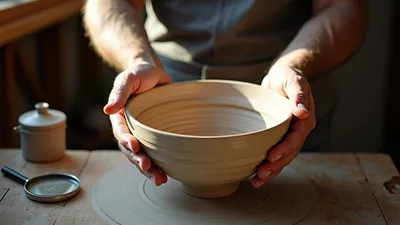
Visual inspection serves as the cornerstone of pottery authentication, with over 95% of restorations detectable through careful examination in bright light.
When you're evaluating a piece, you'll want to start by finding a well-lit area where you can thoroughly examine every inch of the surface. Pay close attention to the crazing patterns and glaze texture, as these details often reveal telltale signs of repairs or restoration work. Examining pieces while they are tilted under lighting helps identify imperfections in the glaze more effectively.
You'll find that holding semi-translucent pieces up to a bright light can be quite revealing – it's almost like playing detective! Look for areas where the translucency doesn't match, as this often indicates a repair job.
Don't forget to check the glaze finish carefully; even the smallest inconsistencies can point to previous restoration work. If you're serious about identifying good pottery, you'll need to train your eye to spot subtle differences in color, texture, and surface quality.
Understanding Pottery Materials
When you're examining pottery, the clay body's composition tells you a lot about its quality and durability.
Each clay type's physical properties are determined by its alumina and silica content, which affects the final product's strength and character.
You'll notice different clay types have distinct weights and densities – for instance, porcelain feels lighter and more refined than stoneware, while earthenware has a particularly heavier, more substantial feel in your hands.
Understanding these material differences will help you determine whether you're holding a delicate piece of fine china or a sturdy piece of stoneware that's perfect for everyday use.
Clay Body Composition
A clay body's composition forms the foundation of every successful pottery piece. When you're examining pottery, understanding the clay makeup helps you recognize quality craftsmanship. The combination of different clay types, like ball clays and kaolin, creates unique characteristics that affect the final product's durability and appearance.
You'll want to look for these key indicators of a well-composed clay body:
- Even particle distribution, which you can spot through the piece's consistent texture and smooth surface
- Proper thermal properties, visible in how well the piece has maintained its shape after firing
- Balanced plasticity, shown by clean, well-defined edges and forms
Think of clay composition like baking a cake – you need just the right mix of ingredients for success. The primary components (alumina, silica, and chemically bound water) work together like flour, eggs, and butter. The addition of fillers and fluxes helps control shrinkage and ensures proper vitrification during the firing process.
When you're checking out pottery pieces, run your fingers along the surface – a good clay body composition will give you a uniform feel without rough spots or inconsistencies. The right blend of materials guarantees that your pottery won't just look great but will also stand the test of time.
Density and Weight Factors
Beyond the clay body's composition, mastering density and weight factors will help you identify quality pottery pieces. You'll want to look for pieces that feel substantial but not overly heavy, as this indicates proper clay usage and skilled craftsmanship.
When you're examining pottery, remember that porcelain typically has a density between 2.1 and 2.6 g/cm³, while regular clay bodies can range from 0.19 to 2.15 g/cm³. The low porosity rate in well-made porcelain contributes to its higher density values. For instance, the Enchanted Forest Porcelain Mushroom Ring Holder showcases the luxurious qualities of porcelain with its gold lustre accents.
You can spot well-made pottery by its balanced proportions and harmonious flow. If a piece feels too heavy, it might mean the potter used excess clay, which isn't ideal. On the flip side, if it feels unusually light, it could be prone to breakage.
Here's a fun tip: try lifting similar-sized pieces to compare their weights – you'll start developing an intuitive sense for what's "just right" (yes, like Goldilocks!).
Professional potters understand these factors instinctively, carefully controlling the amount of clay they use to achieve the perfect balance between functionality and form.
They'll consider both apparent density (what you can see) and true density (including those hidden spaces) to create pieces that are both beautiful and practical.
Glaze Quality and Finish
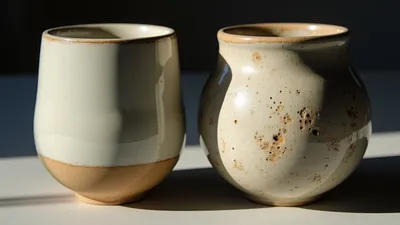
When you're checking a piece of pottery's glaze quality, you'll want to run your fingers along the surface to feel for a consistently smooth finish without bumps or rough patches.
You can spot a well-applied glaze by looking for an even coating that's not too thick at the bottom (which might indicate running) or too thin at the edges (which could mean poor application).
High-quality glazes should incorporate clay and silica content to ensure long-term durability.
The best glazes will have a uniform appearance and be free from common defects like pinholing, crawling, or crazing – think of it like checking a paint job on a car, where you're looking for that perfect, flawless finish.
Glaze Thickness Indicators
Determining the right glaze thickness can make or break your pottery's final appearance and durability. You'll want to pay close attention to how your glaze looks and feels before firing, as proper thickness guarantees even coloration and prevents common defects.
Different types of pottery require different approaches – transparent glazes need a thin, even coat, while majolica demands a much thicker application. Dipping techniques tend to provide the most uniform coverage compared to brush application methods.
Here's what to look for when checking your glaze thickness:
- Check the surface coverage – you shouldn't see any bisque showing through, but the glaze shouldn't pool in recessed areas either.
- Run your fingers across the surface – it should feel smooth but not too thick or bumpy.
- Hold the piece up to light – any inconsistencies in thickness will be more visible.
You'll find that measuring tools like the Anderen Glaze Thickness Penetrometer can help you achieve consistent results, but don't worry if you don't have specialized equipment.
Many experienced potters rely on visual cues and touch to gauge thickness. Remember, factors like bisque temperature, dipping time, and the glaze's specific gravity all play important roles in achieving that perfect coating.
Surface Defect Assessment
A thorough assessment of surface defects stands as the next key step after mastering glaze thickness. You'll want to examine the pottery's surface carefully, looking for any signs of stress concentrations in grooves or unwanted marks that might affect the piece's durability. Think of it as giving your pottery a health check-up!
When you're checking for surface defects, you'll find that modern technology has made things much easier. While you mightn't have access to fancy CT scans or laser microscopy (unless you're a pottery superhero!), you can still perform reliable visual inspections. Today's ceramics industry employs data analytics systems to detect even the smallest surface imperfections.
Run your fingers along the surface to feel for inconsistencies, and look closely for any color variations or textural changes that might indicate underlying issues.
Don't forget to check how the glaze holds up under different conditions. A quality piece should resist those pesky metal marks and maintain its appearance after exposure to acidic substances.
If you're really thorough, you might even want to test the piece's dishwasher resistance – because let's face it, hand-washing everything isn't always practical in today's busy world!
Testing Weight and Density
Testing a pottery piece's weight and density will tell you volumes about its quality and craftsmanship.
You'll want to assess these characteristics carefully, as they're essential indicators of the piece's structural integrity and overall durability. While you don't need fancy equipment at home, there are simple ways to evaluate a pottery piece's density that'll help you make informed decisions. Professional ceramic manufacturers often use density meters and pycnometry for precise measurements.
Here are three reliable methods you can use to test pottery density:
- Compare similar pieces – Hold two similar-sized pieces and notice if one feels markedly lighter, which could indicate poor compaction or high porosity.
- Water absorption test – Place a drop of water on the surface and time how quickly it's absorbed (faster absorption usually means lower density).
- Tap test – Gently tap the piece with your fingernail and listen for the sound; well-fired, dense pottery produces a clear, bell-like ring.
When you're examining pottery, remember that consistent density throughout the piece is just as important as overall weight.
You don't want to find spots that feel lighter or more porous than others, as these variations can signal potential weak points in the ceramic structure.
Examining Surface Texture
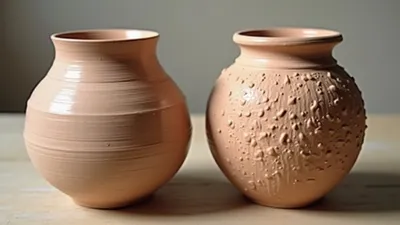
Surface texture serves as a key window into a pottery piece's authenticity and craftsmanship. When you're examining handmade pottery, you'll notice telltale signs like unique finger marks on the bottom and the charming irregularities of stoneware clay. A great example of this is the Squiggles and Dots Porcelain Ring Holder, which showcases its hand-illustrated design beautifully.
The artistic control levels can vary significantly during the firing process. Don't be surprised to find unglazed bottoms with raw clay texture – that's actually a good sign!
You'll want to run your fingers across the surface to feel the different textures created by various techniques. Look for those lovely ripples from throwing marks, or the intricate patterns made by lace rolling and paper resist methods.
If you spot tiny glaze bubbles or see variations in the glaze thickness, you're likely holding a handmade piece. Those little "imperfections" are what make it special!
Pay attention to exposed seams and layered textures that come from hand-building techniques like paddling and coiling. The Squiggles and Dots Porcelain Ring Holder is a prime example where these features come together elegantly.
When you find pieces with wood ash inclusions or charcoal specks in the glaze, you're looking at pottery that's been crafted with traditional firing methods.
These distinctive characteristics aren't flaws – they're the beautiful signatures of an artisan's touch.
Sound Testing Your Pottery
Through careful sound testing, you can quickly assess a pottery piece's structural integrity. When you tap a ceramic piece with a small wooden mallet or even your knuckle, you'll hear distinct sounds that reveal hidden defects. A clear, bell-like ring typically indicates a well-made, crack-free piece, while a dull, thudding sound suggests potential problems lurking beneath the surface. Tapping with a ring helps determine the level of vitrification in the pottery.
Here's what to listen for when testing pottery:
- A high-pitched, resonant ring means you've got a solid piece with no internal cracks.
- A flat, dead sound could signal internal damage or poor construction.
- A slightly muffled but still clear tone might indicate minor imperfections that aren't deal-breakers.
You don't need fancy equipment or years of experience to perform this test – it's something pottery enthusiasts have been doing for generations.
Just find a quiet spot, hold the piece gently, and give it a light tap near the rim. Remember, you're not trying to break any records for the loudest ping – a gentle touch is all you need to hear the telling sounds of your pottery's quality.
Spotting Expert Craftsmanship
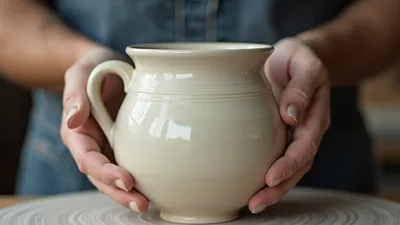
While sound can reveal internal quality, expert craftsmanship leaves visible marks that tell a pottery piece's full story. When you're examining a piece, start with the glaze – it's like the potter's signature. You'll want to look for even application, consistent thickness, and intricate decorative patterns that showcase their skill.
Next, turn the piece over and check out its base. Those unglazed areas and pontil marks aren't just random features – they're telltale signs of how it was made. You'll often find that expertly crafted pieces have smooth, symmetrical rims and handles that feel just right in your hands.
Don't forget to notice the weight; traditional pieces typically have substantial bases that give them stability. The relationship between form and function in pottery design has been vital to human civilization for thousands of years.
The materials used can also speak volumes about the potter's expertise. High-quality clay, natural pigments, and regional materials often point to traditional craftsmanship.
If you're looking at an older piece, check for natural aging signs in unglazed areas – they'll help confirm authenticity.
Symmetry and Balance Assessment
Balance and symmetry stand as fundamental indicators of a potter's skill level and artistic intent. When you're scrutinizing a piece of pottery, you'll want to look closely at how the artist has handled these elements, as they can tell you quite a bit about both the technical mastery and creative vision behind the work.
Whether perfectly symmetrical or intentionally askew, a well-crafted piece will show clear purpose in its design. Potters often draw inspiration from nature's dual qualities when creating their pieces.
Here are three key things to look for when evaluating symmetry and balance in pottery:
- Check the rim's evenness by placing the piece on a flat surface and viewing it at eye level – any wobbles or dips might indicate rushed craftsmanship.
- Look for intentional asymmetry versus accidental flaws – purposeful variations will feel harmonious, while mistakes often appear awkward.
- Examine how visual elements balance each other – a large curved section might be perfectly counterweighted by a smaller, more detailed area.
Functional Design Elements
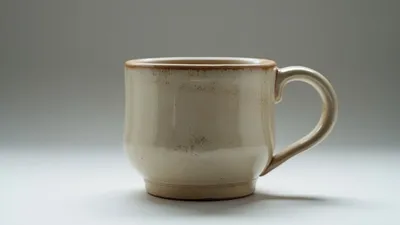
Beyond aesthetic appeal, functional pottery must excel in practical design elements that enhance its everyday usability. When you're examining a piece, pay attention to how it feels in your hands – a well-crafted item should feel natural and comfortable, not awkward or cumbersome.
Look closely at the handles of mugs and pitchers. They shouldn't just be pretty; they need to accommodate your fingers comfortably and stay cool enough to hold when the vessel contains hot liquids. This integration of function and aesthetics creates a more satisfying user experience.
You'll want to check if the piece's weight feels balanced and appropriate for its intended use – nobody wants a top-heavy vase that's prone to tipping!
The mouth of drinking vessels should be just right – not so wide that you'll spill your morning coffee, but not so narrow that you'll bump your nose while sipping.
Run your fingers along the edges and surfaces; they should be smooth and pleasant to touch, without any rough spots that might catch on your skin or make unpleasant sounds against your table.
Firing Temperature Signs
Recognizing firing temperature signs helps you assess the quality and durability of pottery pieces.
When you're examining pottery, you'll notice that different firing temperatures create distinct characteristics in the clay body. Higher firing temperatures typically result in stronger, more durable pieces, while lower temperatures produce more porous ceramics that might be perfect for planters but less ideal for dinnerware. For optimal durability, earthenware requires glazing due to its porous nature when fired at lower temperatures.
Here are three key temperature indicators you can look for:
- Check the clay's density by tapping it lightly – high-fired pieces like stoneware and porcelain (2300°F+) produce a clear, bell-like ring, while lower-fired earthenware sounds duller.
- Look at the surface texture – well-vitrified pieces fired above 1832°F feel smooth and glassy, while lower-fired pieces might feel slightly rough or chalky.
- Examine the color and transparency – hold thin porcelain up to light, and you'll notice translucency if it's been fired above 2372°F.
You don't need to be a technical expert to assess firing quality.
Final Thoughts
Much like finding your perfect dance partner, selecting quality pottery requires attention to both technical details and artistic grace. You've now got the tools to spot masterful ceramics – from examining surface textures to evaluating proper firing temperatures. Whether you're a collector or casual buyer, you'll know what to look for when inspecting pottery's weight, symmetry, and craftsmanship. Trust your trained eye and instincts to guide you toward pieces that'll stand both time and use.