To guarantee your handmade pottery is safe for drinking, you'll need to focus on three key elements: food-safe glazes, proper clay vitrification, and thorough testing. Start by using lead-free glazes and commercial clays tested for safety, then fire your pieces at high temperatures (around 2,300°F to 2,700°F) for complete vitrification. Don't skip testing – check for crazing, conduct water absorption tests, and use the lemon juice method to verify glaze stability. Remember, bright orange and red glazes can be risky due to potential lead content. Your commitment to these safety steps will open up a whole new world of creating trustworthy drinking vessels.
Understanding Food-Safe Glazes
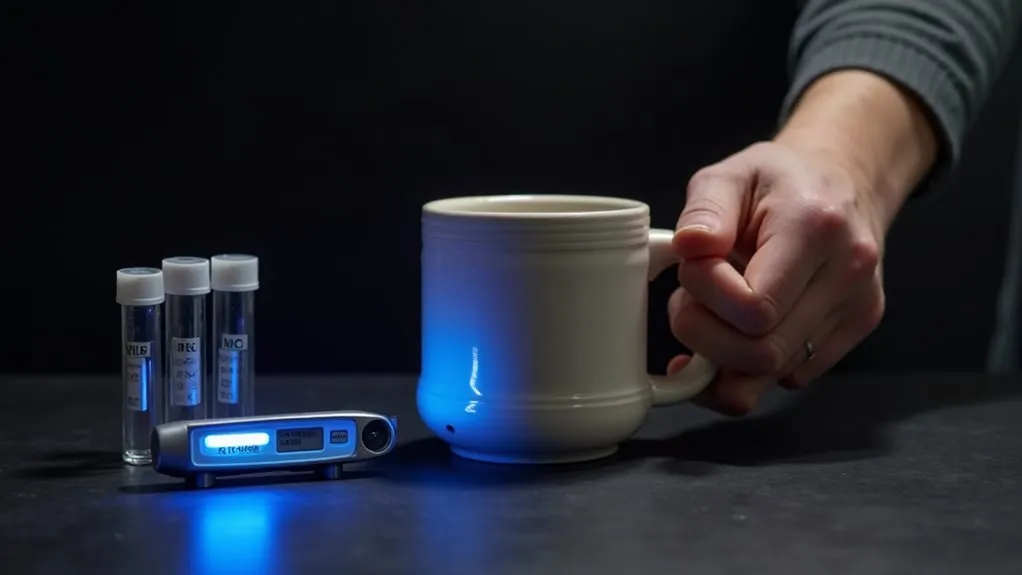
When creating pottery for drinking vessels, understanding food-safe glazes is vital for both safety and functionality.
You'll want to master glaze application techniques that guarantee a smooth, crack-free surface while paying close attention to your glaze composition analysis to avoid harmful materials like lead and cadmium. Using a lead-free glaze like Penguin Pottery Clear Glaze ensures your pottery meets safety standards.
Think of your glaze as a protective shield – it needs to be chemically stable and fully vitrified to keep your drinks safe.
You'll find that proper firing temperatures are important, as they'll determine whether your glaze forms that perfect waterproof barrier you're looking for.
Don't skip the details when it comes to silica content and metal oxide percentages – they're the building blocks of a reliable glaze.
Testing Your Ceramic Pieces
When you're checking your handmade pottery for safety, you'll want to start by examining the surface for crazing – those tiny, spider-web cracks that can make your piece unsafe for drinking.
To test for water absorption, you can mark the water level in your ceramic piece and check if it's dropped after 24 hours, which could indicate your pottery isn't fully vitrified.
You can also run your fingers across the surface to feel for any rough patches or crackling that might've developed during the firing process, as these could be early warning signs of potential safety issues. Conducting a lemon juice test by leaving citrus juice in your pottery overnight can help determine if harmful substances are leaching from the glaze.
Check For Crazing Signs
Before using handmade pottery for drinking, you'll need to check for crazing – a network of tiny cracks that can develop in the glazed surface. While these tiny lines might look artistic, they're actually a sign that your pottery isn't safe for beverages.
Trapped food particles and bacteria can accumulate in crazing cracks over time, making the piece unsafe for use.
Crazing causes include mismatched clay and glaze shrinkage rates, temperature changes, or even rough handling.
You can easily spot crazing through a simple visual inspection. Hold your piece up to good lighting and look for any hairline cracks in the glaze.
For crazing prevention, make sure you're buying from potters who carefully match their clay bodies and glazes, and fire their pieces to proper maturity.
It's also smart to avoid exposing your pottery to extreme temperature changes, which can trigger these unwanted cracks.
Water Absorption Test Methods
To guarantee your handmade pottery is truly safe for drinking, you'll need to perform a water absorption test.
You've got two reliable methods at your disposal: the boiling method and the vacuum method. The boiling method's your go-to DIY approach – simply boil your piece for two hours, let it soak, and compare its weight before and after. These tests also measure apparent porosity of your ceramics. Think of it as giving your pottery a spa day while checking its safety!
The vacuum method's more high-tech, using special equipment to remove air from your ceramic's pores before filling them with water. While it's super accurate, it's typically used in professional settings.
Whichever method you choose, you're looking for low absorption rates – ideally less than 3% for drinking vessels, putting you in that sweet porcelain-grade territory for prime safety.
Clay Body Selection Matters
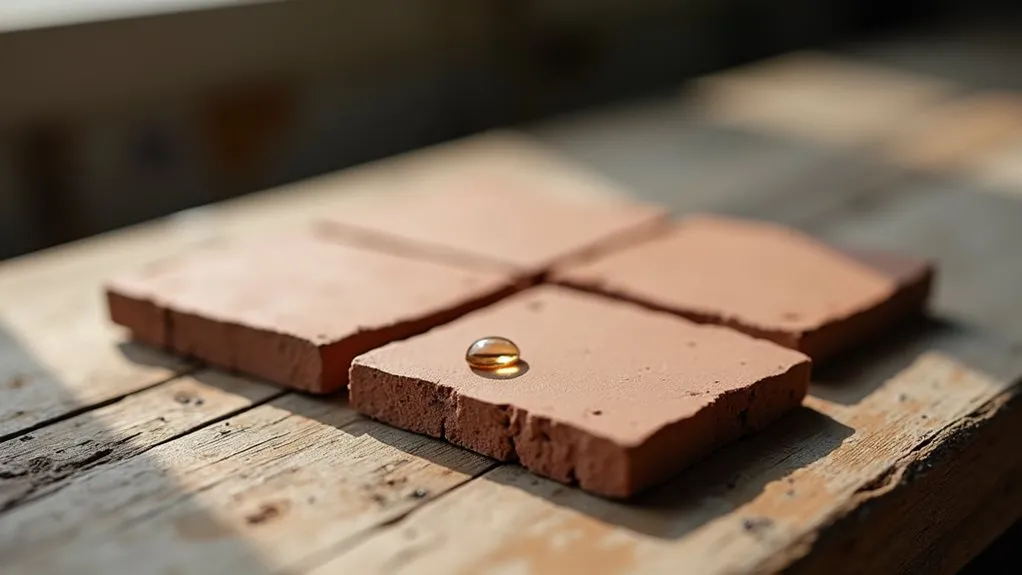
Since your choice of clay body directly impacts the safety of your drinking vessels, understanding absorption rates and vitrification is essential.
Testing your clay for heavy metal content is crucial, as natural clays can contain harmful elements like lead and arsenic.
When you're selecting clay body types, you'll want to focus on those that achieve proper vitrification, reaching an absorption rate of less than 0.5%. Think of your clay like a sponge – the less water it absorbs, the safer it'll be for your beverages.
You can easily test your clay's absorption properties at home through a simple boiling test. Just weigh your fired piece, boil it in water, and measure the weight difference.
If you're working with commercial clays, you're in luck – they're usually pre-tested for safety. However, don't assume all clay bodies are suitable for drinking vessels. Your safest bet is choosing a clay that's specifically formulated for functional ware.
Safe Studio Practices
Safety in your pottery studio starts with proper setup and organization.
You'll need to establish clear systems for storing toxic materials, managing clay dust, and maintaining your equipment. Smart studio organization isn't just about tidiness – it's about creating a workspace where you can focus on your craft without worrying about health risks. Working near open windows and doors promotes essential ventilation for a safer studio environment.
Your safety gear deserves special attention, too.
Don't skimp on PPE maintenance – those respirators and protective eyewear are your first line of defense against hazardous materials. Make sure you're wearing closed-toe shoes and keeping those gloves handy.
Remember, you can't create your best work if you're not taking care of yourself first!
Set up a cleaning schedule, keep your MSDS sheets accessible, and make sure everyone in your studio knows the emergency procedures.
Your creativity flourishes when you're working in a safe environment.
Proper Firing Techniques
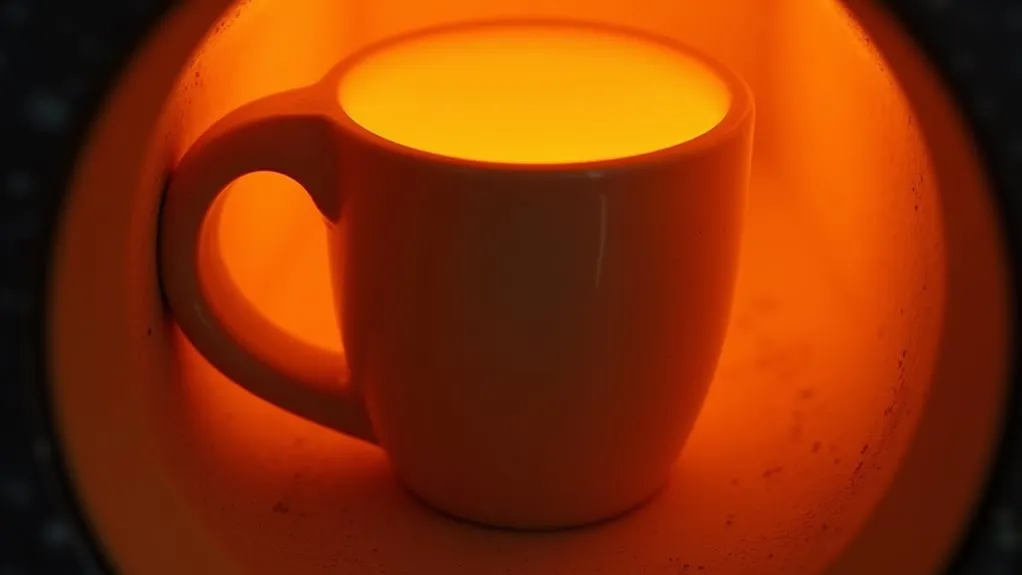
When you're firing pottery for drinking vessels, you'll need to watch for key signs that your clay has reached proper maturity, including a slight sheen and the right amount of shrinkage.
You'll want to follow the temperature guidelines specific to your clay type, typically ranging from cone 6 to cone 10 for stoneware that'll be food-safe.
Getting these firing techniques right isn't just about making pretty pots – it's about creating vessels that'll keep you and your guests safe while enjoying your favorite beverages. Monitor your kiln's temperature closely during the initial heating stages to prevent any issues that could compromise your pottery's safety.
Temperature Range Guidelines
Understanding proper firing temperature ranges stands essential for creating safe drinking pottery.
You'll want to aim for high-fire temperatures between 2,300°F and 2,700°F to guarantee your pieces are truly food-safe. Choosing electric or gas kilns will give you the most reliable control over these crucial temperatures. While it might be tempting to cut corners with lower firing temperatures, you're risking pottery safety if you go below these recommended ranges.
Think of it this way: your clay needs to reach that sweet spot at Cone 10 (2,381°F) to become fully vitrified – that's when the magic happens!
Lower temperatures might leave you with porous pieces that aren't suitable for your morning coffee or evening tea.
And while alternative firing methods like Raku might create stunning pieces, they won't give you the dense, non-porous results you need for safe drinking ware.
Clay Body Maturity Signs
Now that you know the right temperature ranges, spotting signs of proper clay body maturity becomes your next key skill.
You'll want to watch for key indicators during the vitrification process to guarantee your pottery's safe for drinking. Think of it as your clay's way of telling you it's reached the sweet spot in its firing range.
Proper clay, flux, and filler ratios in your clay body enhance these maturity signs. Here's what a perfectly mature clay body looks like:
- The surface feels smooth and solid, without any chalky or rough patches
- There's no visible warping or distortion in the piece's shape
- The color is uniform and matches what you'd expect for your clay type
- When tapped, it produces a clear, bell-like ring instead of a dull thud
These signs tell you you've achieved the right balance of temperature and time, creating a safe, durable piece.
Regulatory Standards for Drinking Vessels
Since consumer safety is vital, the FDA maintains strict regulatory standards for pottery intended for food and beverage use.
When you're crafting drinking vessels, you'll need to guarantee regulatory compliance by following specific guidelines, particularly regarding lead content and labeling requirements. Just like marine vessel operators must comply with strict testing protocols, pottery makers have their own set of mandatory safety requirements.
You'll want to pay special attention to your glazes, especially if you're using bright orange, red, or yellow colors – these can be risky due to potential lead content.
If you're making decorative pieces that aren't food-safe, you must clearly label them as "Not for Food Use—May Poison Food."
And here's something important to remember: no amount of washing or treatment can make unsafe pottery safe for drinking, so it's important to get it right from the start.
Your customers' safety depends on your attention to these standards.
Final Thoughts
You'll find that creating food-safe pottery isn't just about following rules – it's about mastering your craft with care and attention. By selecting the right clay, using proper glazes, testing your pieces, and following safe studio practices, you're setting yourself up for success. Remember, whether you're a beginner or seasoned potter, your commitment to safety guarantees that your handmade vessels bring joy, not worry, to those who drink from them.